Meshfree CFD Software for Evaluating the Behavior of Liquids
Particleworks is a CFD simulation software for evaluating the behavior of liquids such as water and oil. Particleworks is widely used in various industrial sectors, from automotive and aerospace to consumer goods, through power generation to the Food & Beverage industry.
MESHfree CFD tool
User Interface
Particleworks’ intuitive user interface lets you handle an entire simulation, from pre-processing through post-processing. You don’t have to be an expert to edit simulation parameters or keep track of multiple projects.
The 3D view window features ultra-fast, high-quality OpenGL rendering optimized for large-scale simulation with millions of particles. The window system is highly customizable, letting users compare multiple results side by side. Both Windows and Linux are supported.
Simulation Flow
Steps of the simulation flow
- Step1 – Modeling
Import CAD data and define the resolution for pre-processing.
The STL, OBJ, and NASTRAN formats are supported. - Step2 – Condition Settings
Simply apply physical properties and movements to the model.
No tedious adjustments are needed for boundary conditions. - Step3 – Simulation
You can accelerate the calculation using multiple CPU cores or GPUs.
Additionally, you can view the results of a simulation while it is still in progress. - Step4 – Post-Processing
Visualize and evaluate the simulation results using various post-processing tools. For example, you can create surface meshes and export CSV and video files.
Applications
- Oil splashing and forced lubrication of transmissions – mechanical and electrical
- Bearings – oil and grease lubrication
- Engine lubrication, gradability analysis, oil separation in breather chambers
- Oil sump aeration
- Piston cooling and E-motors cooling: thanks to the heat transfer capability, Particleworks can predict oil temperature, piston and windings temperature for IC engines and running oil-cooled e-machines
- Interaction between vehicles and water, mud, snow–wading, soiling, and contamination analysis including the aerodynamic effects
- Water turbine for torque and power prediction
- Highly viscous flows – detergents, food, cement, glue, etc.
Capabilities
- Liquid and liquid-gas flow
- Heat Transfer, Heat Conduction in solids, and Conjugate Heat Transfer
- Heat Transfer Coefficient calculation and export
- Internal airflow solver
- Intuitive interface, pre-solution-post in one GUI
- Easy handling and moving parts with 6 degrees of freedom
- Automatic Simulation process and pre-post via Python scripting
- Automatic output of forces and torque (e.g. churning losses)
- Multi-core and multi-GPU calculation
- Powerful flow visualization
- Mapping of pressure and HTC on walls for FEA analysis
- Coupling to Multi-Body and FEA solvers
- Coupling between fluid and solid granular flow (MPS + DEM)
GPU High-Performance Computing
With the addition of the GPU option feature, it enables fast simulations that take advantage of NVIDIA‘s CUDA GPU boards. This can significantly reduce computation time and allow you to perform high-speed calculations on a desktop PC, which is equivalent to supercomputers and HPC servers. Also, a new HPC Pack is available to expand the number of cores for parallel computing. The number of cores can be increased efficiently based on 1 Pack (16 cores). You can also install multiple packs, which allows you to assign packs to different jobs. Also, multiple packs can be installed, allowing you to assign a pack to each job.
Particleworks for Ansys
Particleworks for Ansys is an interface between the liquid flow solver Particleworks and the Ansys suite of software.
The interface allows to integrate Particleworks in the Ansys Workbench, to build a multi physics simulation process and to easily transfer data between Particleworks and SpaceClaim , Fluent and Ansys Mechanical.
By linking SpaceClaim and Particleworks the user can share the geometry between different CAE models, so that the geometry preparation is done only once.
The interface from Particleworks to Ansys Mechanical allows to transfer pressure and Heat Transfer Coefficient maps from the liquid flow analysis to the thermal and stress analysis in Ansys both in steady and transient manner.
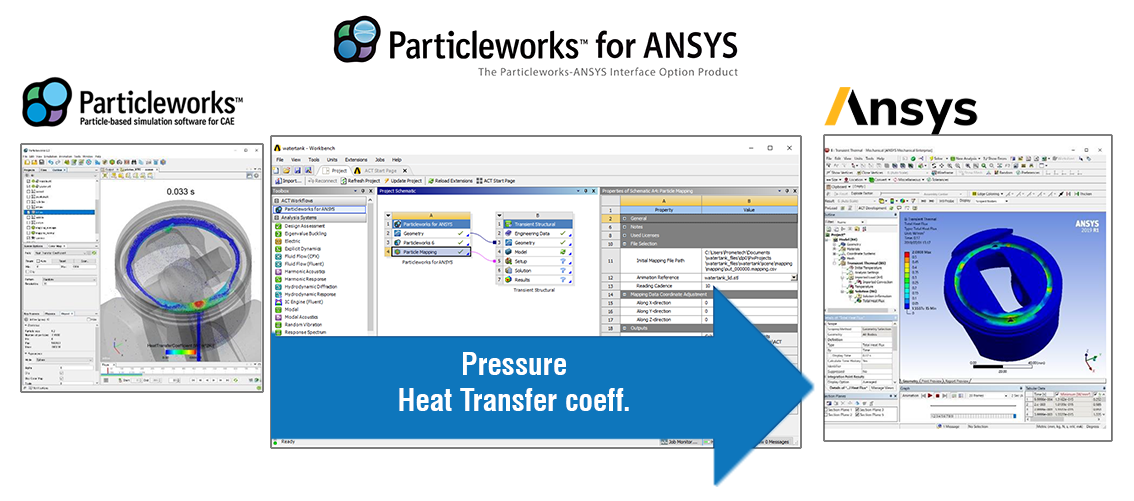
Moreover if the user wants to transfer an air flow field calculated by Ansys Fluent to Particleworks, this can be done in one click, both for a steady and for transient flow conditions. This is for example useful to transfer the aerodynamic field from Fluent to Particleworks to simulate the rain interacion with the car body, wipers, mirrors
Granuleworks
Powder and granular flow simulation
Particleworks is a CAE software for the simulation of liquid flows based on the Moving Particle Simulation method (MPS).
Granuleworks is a Discrete Element Method software (DEM) that allows simulating granular flow and powder by solving Newton’s Equation of motion.
Granuleworks calculates the translation and rotation of each solid particle considering contact, friction, slip and adhesive forces between particles.
Granuleworks is widely used for evaluating manufacturing processes that handle powders in the field of food, pharmaceuticals, chemicals, transport equipment, mining and electronic materials and for design and improvement of powder processing and equipment.
Granuleworks can simulate powder mixing, conveying, storage, filling, compression molding, slurry, granulation, etc.
Key Features
- No mesh generation, import your 3D CAD as is
- Single interface for the entire simulation process, pre-processing, simulation, post-processing
- Scalable Discrete Element Method (SDEM) to simulate fine powder
- Thermal conduction analyses
- GPU/CPU High Performance Computing
- Coupled Simulation with CFD tools and Particleworks
- Coupled Simulation with Multi-body software RecurDyn
Technical Capabilities
- Particle Size Distribution can be user-defined, Log Normal and Rosin-Rammler
- Rolling resistance modelling
- Heat transfer, particle-to-particle and particle-to-walls
- Liquid bridge force for wet powder
- Van der Waals Force
- Scalable Discrete Element Method (SDEM) to reduce the number of particles and computational time while maintaining an equivalent particle behavior
- Coupling with Finite Volume CFD and particle-based MPS to account for fluid-particle interaction
- Elastoplatic materials for powder compression analysis
- Specific models and tuning for materials like snow